Реверс-инжиниринг промышленных смесителей с целью импортозамещения
Делимся опытом реверс-инжиниринга погружного смесителя с целью локализации его производства в России. Подчеркнём, что реверс-инжиниринг является лишь одним из инструментов при импортозамещение.
Задача – разработать комплект РКД на промышленный смеситель
Исходные данные – импортный промышленный смеситель
Результаты работ – комплект конструкторской документации
Сроки выполнения – 4 месяца
- 3D-сканирование и проведение измерений – 10 дней
- Разработка твердотельных 3D-моделей – 14 дней
- Разработка и согласование чертежей – 40 дней
- Модернизация конструкции – 30 дней
- Адаптация под производство заказчика – 40 дней
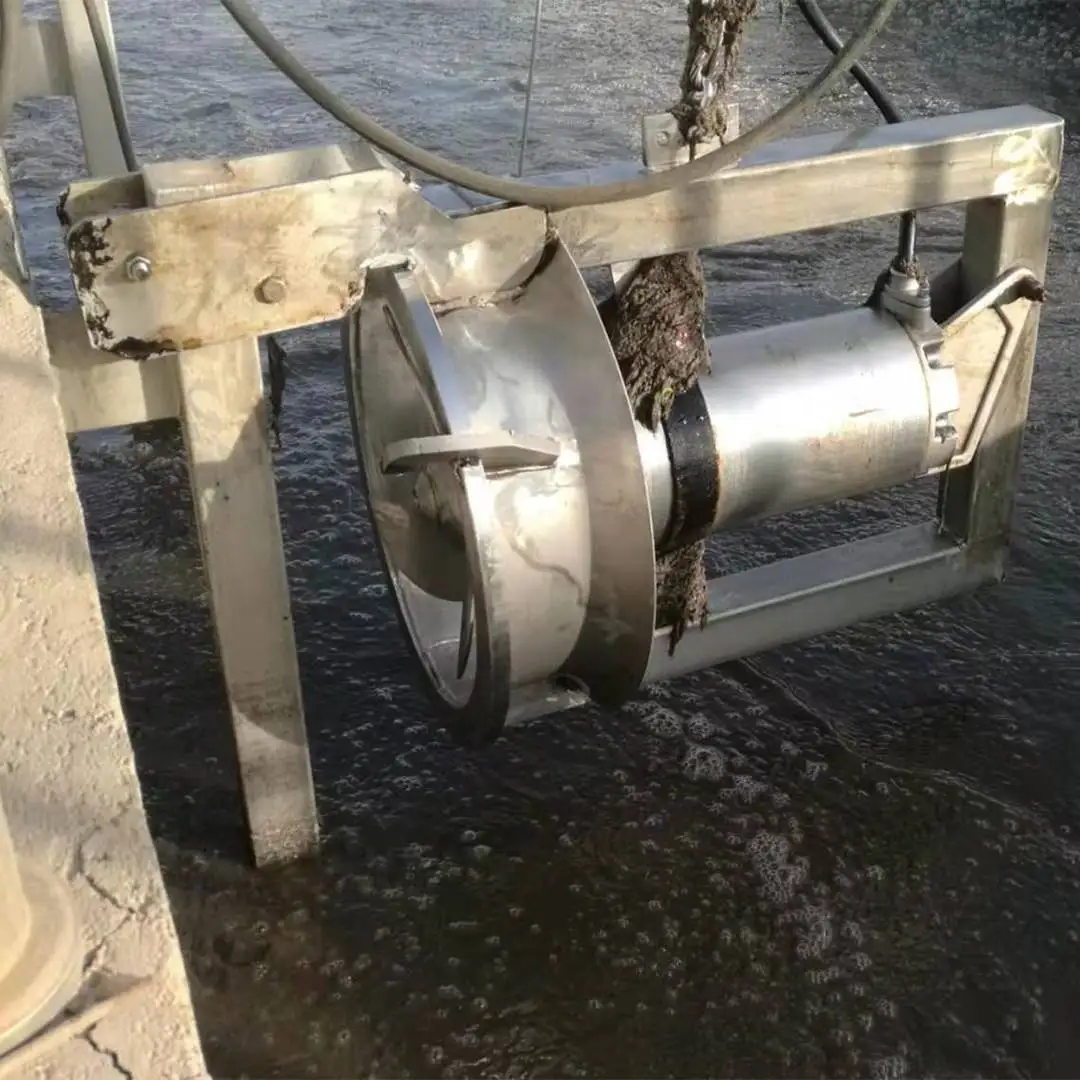
Запрос на реверс-инжиниринг
Перемешивание — важный технологический процесс во многих фазах очистки воды. В зависимости от назначения и требуемого времени смешения могут использоваться различные устройства для перемешивания. Одним из типов перемешивающих устройств является динамическая мешалка пропеллерного типа (погружной смеситель), которая используется для перекачивания вод с малыми напорами и для создания потока в водоёмах.
На данный момент в России наблюдается жёсткий дефицит необходимых деталей для оперативного ремонта мешалок. Раньше их заказывали из Европы, сейчас такой возможности просто нет.
В рамках проекта по локализации одного из видов насосов производства немецкой компании KSB, было необходимо выпустить рабочую конструкторскую документацию, подобрав при этом привод с аналогичными характеристиками и внеся все необходимые изменения в соответствующие детали и узлы с учётом нового привода. Это стало задачей для специалистов инжинирингового центра Самарского университета, к решению которой были привлечены сотрудники нашей компании.
Решение
Перед разборкой насоса было отсканировано всё изделие целиком, за исключением рамы, в которую устанавливается привод с рабочим колесом, чтобы потом при 3D-моделировании сравнить все внешние размеры и взаимное расположение корпусных деталей, а также проверить отклонения построенной 3D-модели от геометрии изделия.
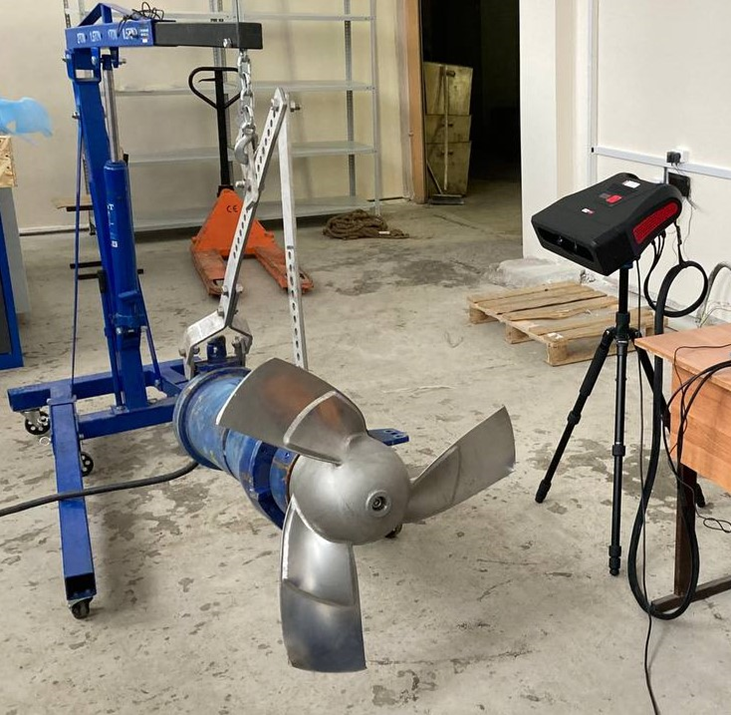
Для создания цифровой копии погружного смесителя был использован сканер RangeVision PRO. Процесс сканирования занял около 4-5 часов, включая нанесение меток, измерение и калибровку. Сканирование действительно позволило нам быстро получить геометрию и использовать её в качестве исходных данных для дальнейшей модернизации конструкции.
После разборки было отсканировано несколько корпусных деталей уже на поворотном столе. На каждую суммарно ушло около 1-1,5 часов. Частично по этим сканам были созданы 3D-модели. Часть измерений проводилась ручным измерительным инструментом, без этого никак не обойтись — это наиболее надёжный способ определить допуска посадочных размеров деталей, но при этом наиболее длительный. Так же никак не обошлось без эскизирования: например, валы измеряли исключительно ручным инструментом. Ручные измерения потребовались бы в любом случае, независимо от того, стали бы сканировать их или нет, поэтому инженеры просто сэкономили себе время.
А вот справиться с измерением рабочего колеса без помощи 3D-сканера вряд ли удалось бы. Диаметр лопаток составляет около 800 мм, но оказалось достаточно отсканировать одну лопатку. Суммарно время сканирования этой детали (матирование поверхности не потребовалось) составило около 1 часа.
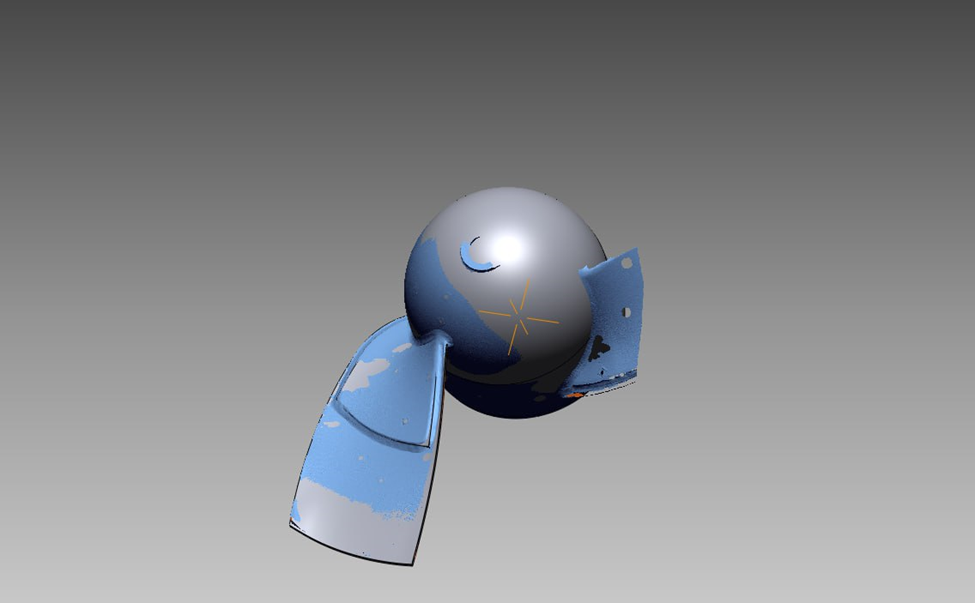
Результат
После завершения сканирования инженерный отдел выполнил работы по реверс-инжинирингу получившихся моделей, была разработана и выпущена конструкторская документация.
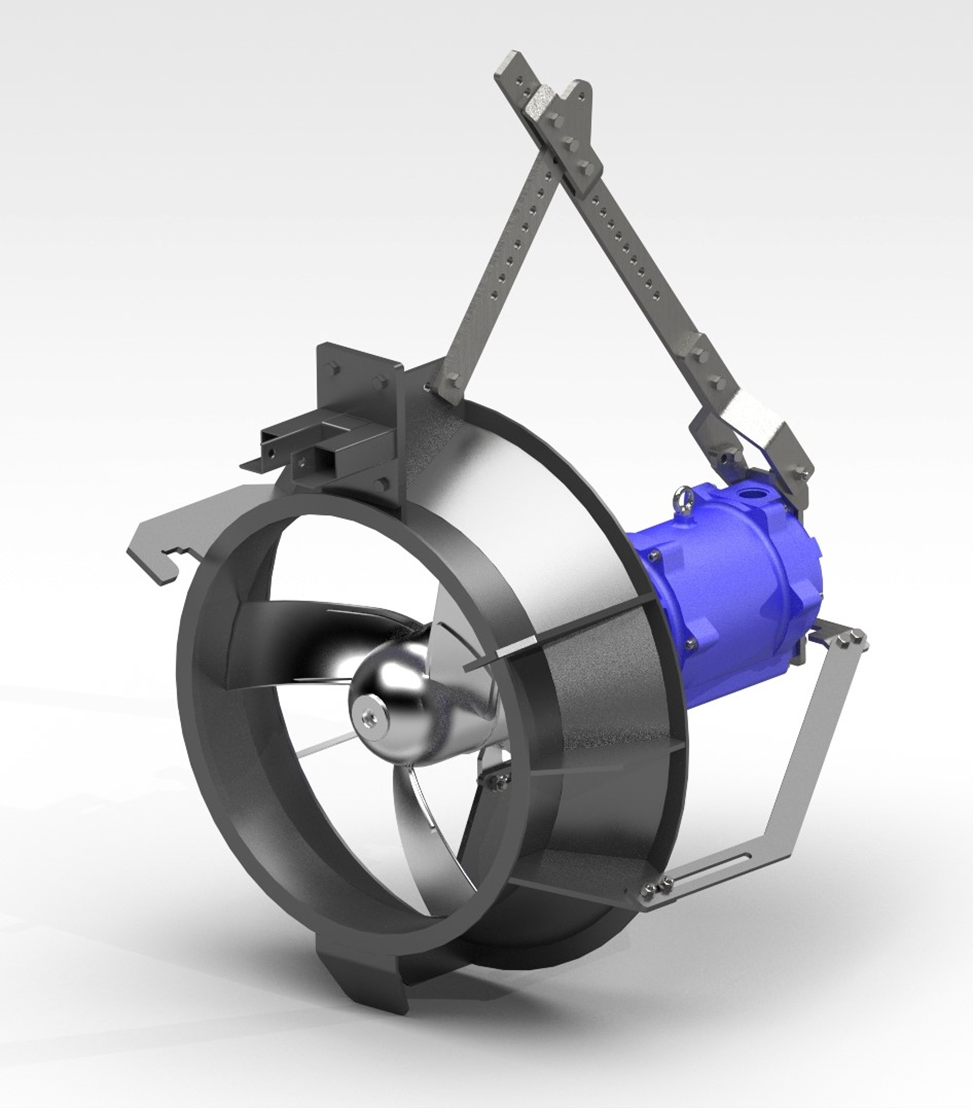
Этот пример отлично показывает как с помощью реверс-инжиниринга возможно создавать аналоги импортной продукции, замещая критически важные недостающие компоненты и продукты для поддержки отечественного производства. Он также помогает сократить сроки разработки продукта, разработать комплект конструкторской документации для дальнейшего производства, а также исследовать конструкцию или дизайн анализируемого продукта.
Использованное оборудование и технологии:
- 3D-сканер RangeVision PRO
- Ручной измерительный инструмент
- Моделирование в инженерном ПО